Techniques
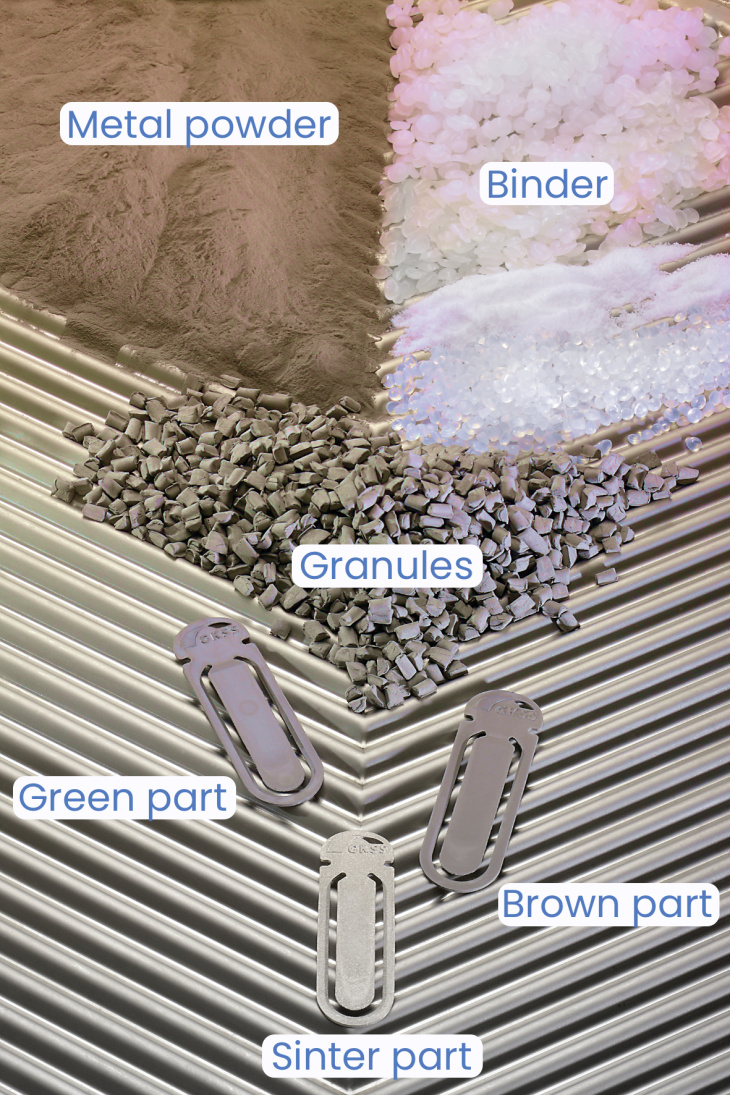
Process chain of binder-based sintering technologies
For the production of test specimens and implant prototypes we apply binder-based sintering technologies, which we enhance and optimize with respect to the special requirements of magnesium and titanium. As basis, we mix fine metal powders (typically: diameter smaller 50 µm) with a combination of different polymers (the so-called binder) in order to produce a shapable mass. This mass can be shaped by various industrially established technologies to the intended geometry of the component, for example by means of injection moulding (MIM: metal injection moulding) in the case of large-scale production. Furthermore, additive manufacturing techniques like Fused Filament Fabrication (FFF) or Fused Granular Fabrication (FGF) can be applied, too. While FFF is the typical technology of home 3D-printers, FGF utilizes as feedstock the same granules as MIM. Independent of the applied shaping technique for manufacturing the so-called green part, as the next processing step the binder is removed (brown part) and a sintering process consolidates the powder to the final metal component (sinter part). For application of these techniques and chracterization of the properties of the produced parts we use the equipment listed in the following. If necessary, it can be complemented by the instruments of the other institutes at Hereon.