Digital Twins
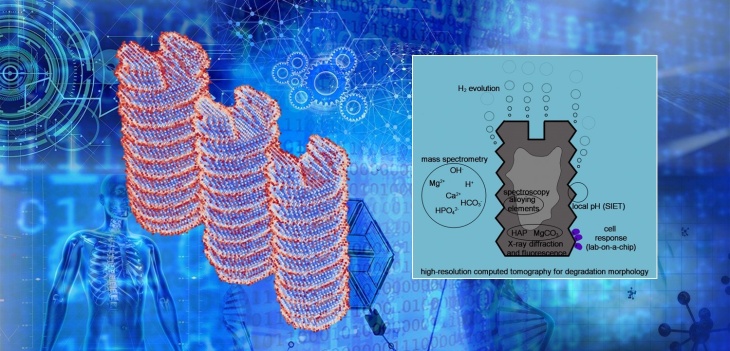
Picture: Digitaler Zwilling. Hereon/N. Huber
Digital twins of materials are comprehensive virtual models, which capture in particular also internal processes as well as interactions of the materials with their environment, for example, during processing or in the field. They thus provide insights which are often not – or only at great expense - accessible in reality. Digital twin digitally resemble in many aspects a set of tailor-made in-situ experiments, which is why the combination of both if often particularly beneficial. At Hereon, digital twins are used to support the development of materials and interpretation of experiments for metallic biomaterials, nanoporous metals and hydrogen storage systems, among others.
- Digital Twin of a nanoporous metal
- Machine learning architecture for identifying chemical compounds for modulating magnesium corrosion in a tailor-made way.
- Digital twin for biodegradable magnesium implants
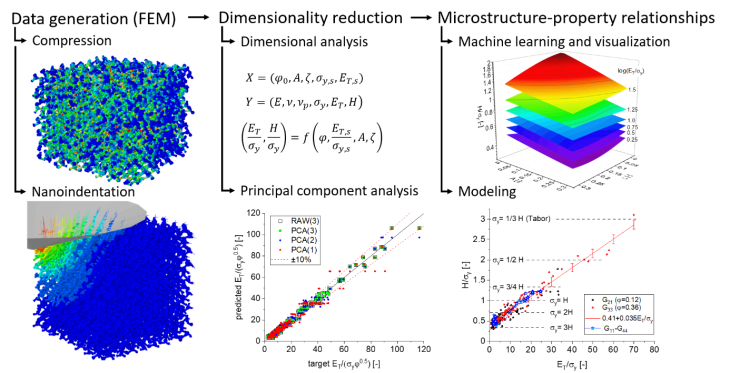
Picture: Digital Twin Nanoporous Metal. Hereon/N. Huber
Workflow for dimensionality reduction of complex microstructure-property relationships for nanoporous metals under uniaxial compression and nanoindentation. Source: N. Huber, Materials 2021, 14(8), 1822. Publication
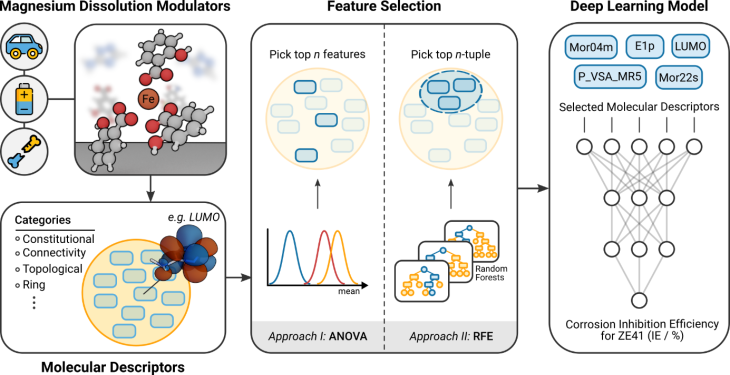
Picture: Machine learning architecture for identifying chemical compounds for modulating magnesium corrosion in a tailor-made way. Photo: Hereon/E. Schiessler
Predicting the inhibition efficiencies of magnesium dissolution modulators using sparse machine learning models Source: Publication
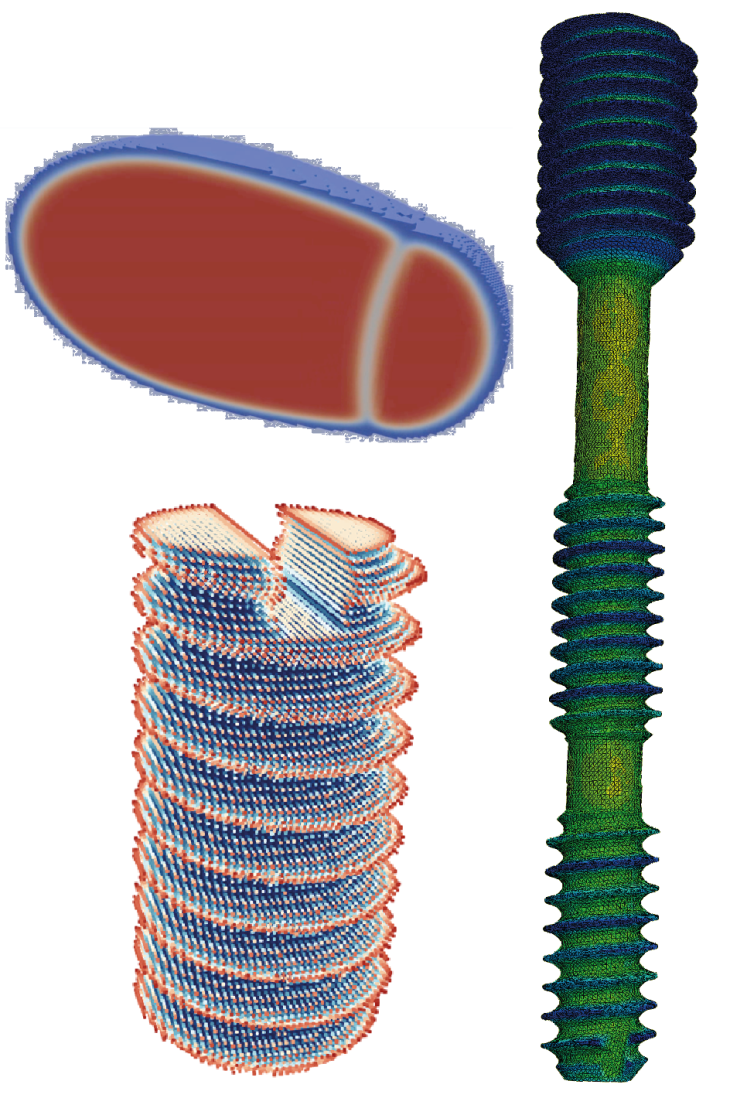
Photo: Digital twin for biodegradable magnesium implants. hereon/D. Steglich
Magnesium alloys have attracted increasing interest as innovative biodegradable materials, particularly for their potential use as temporary orthopedic implants. The degradation of the implants is caused by a corrosive process, in which the implant reduces its mechanical strength. Monitoring, controlling and ideally predicting this process is of significant relevance for clinical healthcare. In a combined experimental-numerical approach the production of implants by sintering (upper left), the corrosion in physiological environment (lower left) and the residual strength of the implant (right) are modeled using phase-field methods, peridynamics and damage mechanics, respectively. This digital twin thus reproduces all stages from production to corrosion and use and thus creates a basis for virtual material development.