AVaiL
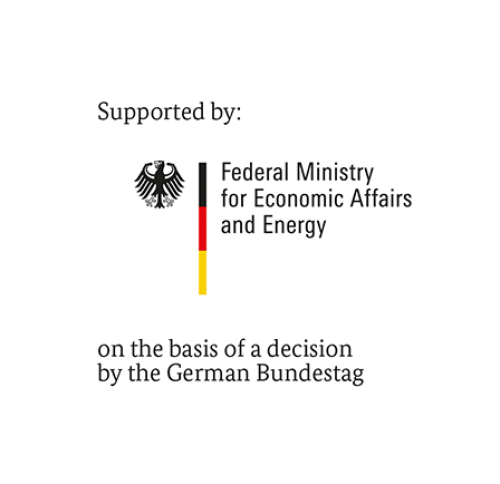
Airbus Aerostructures (ASA),
Automotive Center Südwestfalen (ACS),
Fraunhofer Gesellschaft (FHG),
Premium AEROTEC (PAG),
voestalpine Automotive Components Schwäbisch Gmünd (vACSG)
The overall objective of the project AVaiL-DE is to upgrade processes for the high-rate, cost-efficient and resource-saving production of metallic aerospace structures. The project is based on at least four actual structures that represent a defined range of components and are to be developed to a high level of technical maturity. This overall objective will be achieved via the further development and optimization of three solid-state joining processes, friction stir welding (FSW) and stationary shoulder friction stir welding (SSFSW) respectively, as well as refill friction stir spot welding (refill FSSW) and friction surfacing (FS), to achieve an efficient and cost-effective production of components and assemblies while at the same time increasing structural safety through improved damage tolerance behavior. For this purpose, process-microstructure-property relationships are systematically determined for the three processes, which lead to high-quality joining properties with the shortest possible cycle times. With the development of these joining processes and their introduction in the production of components and assemblies, a weight reduction of 20% and a reduction in production time of 20% should be achieved compared to conventional mechanical fastening technologies. The knowledge gained in the initial phase of the project will be used in the final phase to realize representative examples of integral structures such as a trim spindle box, hybrid aluminium-titanium seat rails and aluminium cross beam spacer.
Objectives of the project at Hereon
Global
- upgrade processes for the high-rate, cost-efficient and resource-saving production of metallic aerospace structures
- further development and optimisation of three solid-state joining processes: friction stir welding (FSW) and stationary shoulder friction stir welding (SSFSW) respectively, as well as refill friction stir spot welding (refill FSSW) and friction surfacing (FS)
- increase of structural safety through improved damage tolerance behaviour
- structural weight reductions of 20% and a reduction in production time of 20% compared to conventional mechanical fastening technologies (e.g. riveting)
- realisation of representative examples of integral structures such as a trim spindle box (SSFSW), hybrid aluminium-titanium seat rails (refill FSSW) and cross beam spacers (FS)
Technological
- realisation of high-speed SSFSW
- realisation of dissimilar aluminium-aluminium as well as aluminium-titanium SSFSW joints
- compilation of a process catalogue, in which the respective process parameters, mechanical properties, weld characteristics (i.e. defects, geometry) for each weld are summarised to support quality control strategies
- development of refill FSSW tools with extended lifetime
- deposition of FS aluminium layers on titanium substrate material
- implementation of robotic FS for three-dimensional builds
- creating technology validators with optimised FSW / SSFSW, refill FSSW and FS processes
Scientific
- understanding of the softening process in front of the tool and material transport during the welding process in high-speed SSFSW
- clarification of the microstructure evolution at the interface between aluminium and titanium during SSFSW
- description of the wear mechanisms on refill FSSW tools
- understanding of the bonding mechanisms in hybrid aluminium-titanium layers generated during FS
Processes and exemplary validators
-----------------------------------------------------------
Stationary Shoulder Friction Stir Welding (SSFSW) and Trim Spindle Box

Schematic illustration of the SSFSW process:
a) tool positioning, b) tool plunge, c) translational tool movement d) tool retraction
Refill Friction Stir Spot Welding (refill FSSW) and Hybrid Aluminium-Titanium Seat Rail

Schematic illustration of the refill FSSW process:
a) tool positioning, b) pin retraction and sleeve plunge, c) pin plunge and sleeve retraction to surface level, d) tool retraction
Friction Surfacing (FS) and Cross Beam Spacer

Schematic illustration of the FS process:
a) Stud positioning, b) plastification of the stud tip (plasticising phase),
c) translational movement and layer deposition (deposition phase), d) stud retraction