MA.D.AM
A Consolidator Grant Project funded by the European Research Council
Summary
With aerospace technologies gaining increased attention due to a continuously growing interest in space, the drive towards innovation in sectors associated with aerospace is now in high gear. Additionally, there is a growing demand in value-added materials for additive manufacturing that promote superior part properties, not achievable by conventional fusion-based routes. The EU-funded MA.D.AM project will address this demand by covering the whole process chain from material development to layer deposition via solid-state processes for the selected use-case of novel Al-Cu-Li alloys. The project will apply a systematic multidisciplinary strategy, including experimental and numerical approaches and combining them via machine learning.
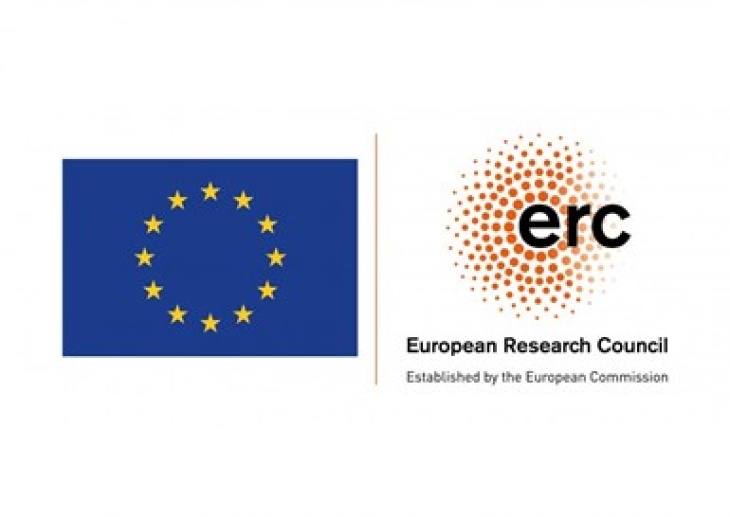
This project has received funding from the European Research Council (ERC) under the European Union’s Horizon 2020 research and innovation programme (grant agreement No 101001567)
Objectives
The MA.D.AM project addresses the strong need of wire-based additive manufacturing (AM) for customized value-added metallic materials that are not established yet. The project aims at establishing novel scientific knowledge for the fabrication of novel wire materials and AM parts with hitherto not reached properties, based on the application of high-strength Al-Cu-Li alloys, as cutting-edge candidates for AM in aerospace applications. For this purpose, innovative solid-state materials development and AM processes are utilized to obtain alloys beyond the known thermodynamic borders. The solid-state Friction Extrusion process allows generating phases under non-equilibrium conditions, leading to so far unexplored microstructural states, enabling to produce novel high-performance wire material with tailored properties. To avoid microstructural deterioration and preserve or even improve the beneficial properties of the designed wires, the Solid State Layer Deposition process is employed. The overarching objective of MA.D.AM is to establish the real-world process chain paired with numerical approaches, leading to a digital twin to achieve a hitherto unavailable decryption of the composition-process-microstructure-property relationships for solid-state materials development and AM. To achieve this objective, a systematic multidisciplinary approach based on the combination of sophisticated physical modelling concepts, advanced experimental approaches including characterization techniques and machine learning is pursued. The selected modelling approaches along computational thermodynamics, microstructure and process modelling, together with special-designed (in situ) experiments will establish a clear link between process characteristics and evolution mechanisms such as phase formation and recrystallization kinetics. The digital twin will be built via a novel hybrid modelling strategy based on experimental and numerical data developed on the concepts of machine learning.
Work Packages
This WP provides the experimental basis to establish a fundamental understanding of the materials development process via the friction extrusion process. Producibility and processability of novel wire materials will be demonstrated. Fundamental insight into material flow during the process will be obtained.
Contact
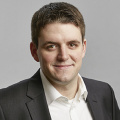
Head of Department
Institute of Materials Mechanics / Solid State Materials Processing (WMP)
Phone: +49 (0)4152 87-2552
Helmholtz-Zentrum Hereon
Max-Planck Straße 1
21502 Geesthacht
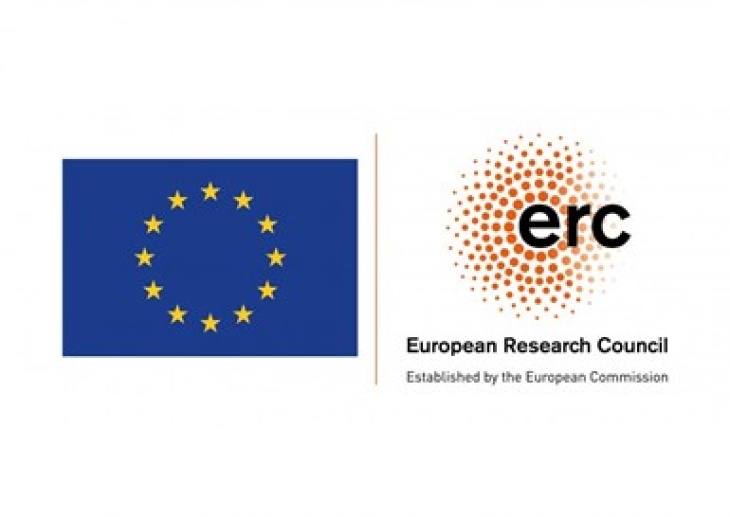
This project has received funding from the European Research Council (ERC) under the European Union’s Horizon 2020 research and innovation programme (grant agreement No 101001567)