A new generation of aircraft: Materials research scientists in Geesthacht are engaged in original scale research on joints
Joining technology specialists at the Helmholtz-Zentrum Geesthacht (HZG) are carrying out research on laser beam welding of a new aluminium-lithium alloy, within the research project LAWENDEL, which is part of the European Aeronautical Research Programme, Clean Sky. The long-term objective of the Clean Sky project is to build lighter and thus more environmentally friendly aircraft.
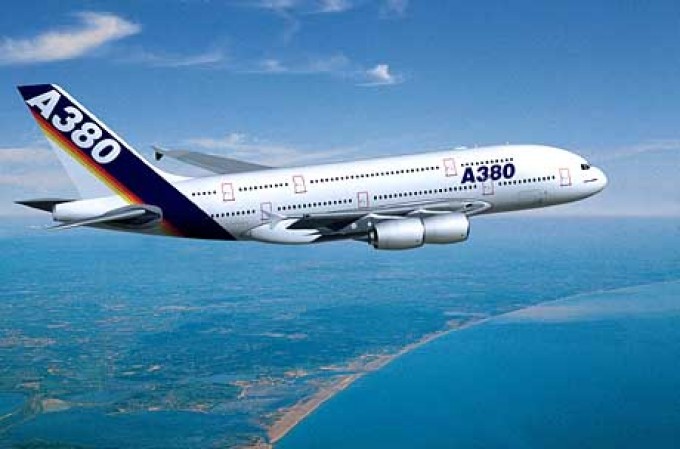
Photo: HZG
Technologies for environmentally friendly aircraft are in great demand in Europe. In order to reduce carbon dioxide (CO2 ) emissions, engineers in the aviation industry are placing an emphasis on weight saving. The lighter the aircraft, the lower the fuel consumption, and CO2 emissions are thus reduced. Weight savings can be made, for example, by using laser beam welding in the assembly of aircraft fuselage structures. This technology is already being employed in the assembly of the Airbus A380. It saves on sealants and rivets so that a weight saving potential of up to 20 percent has been achieved. Research in the Institute of Materials Research at the HZG includes joint technologies for the next generation of aircraft.
Dr. Nikolai Kashaev, a materials research scientist at the Helmholtz-Zentrum Geesthacht explains: “We are examining the joint weld of a newly developed aluminium-lithium alloy. In the course of these investigations we are obtaining information regarding process parameters. Moreover, we are comparing the mechanical behaviour of the new alloy with conventional aluminium alloys”. The term alloys refers to a mixture of several chemical elements. The new alloys could mean further weight saving of up to ten percent in comparison with the joints which are currently in use. In order to achieve this, the research scientists in Geesthacht have scaled up the process technologies developed for the welding of lightweight construction demonstrators to original size. They have constructed model components on which they can examine results with regard to implementation feasibility.
150,000 euro have been made available for the EU project LAWENDEL (Laser welding of newly developed Al-Li alloy). The project partner is Manchester University which is undertaking the task of model based process design within the project. This project commenced in January 2013 and will run for 20 months until August 2014.
Clean Sky
Clean Sky is a European aeronautics programme in which new groundbreaking technologies for cleaner and quieter aircraft will be developed. By 2020, the joint technology initiative, Clean Sky, plans to reduce CO2 emissions by 50 percent, nitrogen oxide emissions by 80 percent and noise pollution by 50 percent per kilometre flown and per passenger. A kind of ecological environmental life cycle is also to be introduced for the materials and components of the aircraft, which will take development, production, service and disposal/recycling into account. The initiative has a total of 1.6 billion euro at its disposal. More than 400 participants from the fields of science and industry are actively involved in the Clean Sky project.
Further information
Information on laser beam welding at the HZG
The HZG “Joining and Assessment” department is concerned with issues relating to laser beam welding process development, which include process simulation, the development and construction of lightweight demonstrators and also their testing and assessment with respect to their damage tolerance performance. In 2010, a large-format laser welding installation was commissioned for this purpose. 18 employees are presently engaged in research in this department.
Information on demonstrators
In order to assess the fatigue and fracture performance of welded lightweight construction components, the complex loading conditions and local variations in mechanical properties and residual stress distribution in the welded joint area must be taken into account. As the size of welded components has increased, the costs of production and testing have become a significant factor. Simulation based process development is becoming increasingly important in order to minimise these costs. The construction of a demonstrator provides conclusive experimental evidence of successful development. A demonstrator is a model component which demonstrates implementation feasibility within the scope of a project.