Research
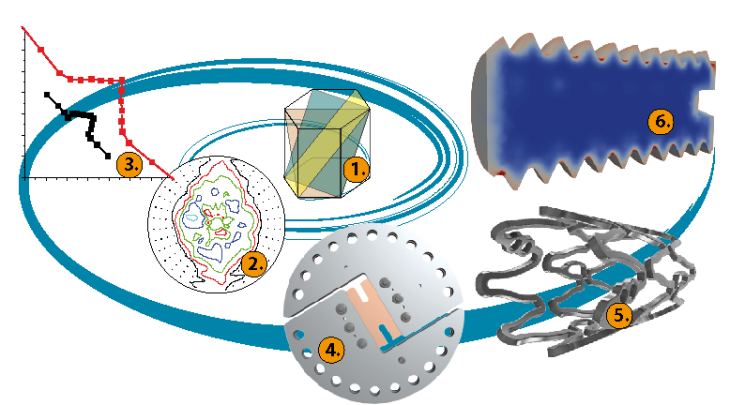
modelling activities for magnesium-based products
Magnesium alloys are promising candidate materials for products in the transportation industry. Due to their low weight and high strength they can contribute to reduce the mass of vehicles and therefore limit their CO_2 emission .
The application of magnesium alloys demands for reliable simulation tools for predicting the forming capabilities, the structural responses to mechanical loads, and the lifetime of the components. The predictive models have to match the distinctive mechanical characteristics attributed to the low-symmetric hexagonal close-packed metal, which demands for up-to-date material laws. The selection of an appropriate yield function capturing inelastic (permanent) deformation under multi-axial stress states challenges many researchers. The prediction of damage events and material failure is a research topic on its own.
Furthermore, Mg alloys are also emerging as viable biodegradable materials for e.g. bone screws and stents. Since the desired degradation and resorption of the implant material reduces the mechanical strength of the implant, its load carrying capacity at all times has to be computed. Monitoring the decline of the load carrying capacity of an implant, as the degradation progresses, is of significant relevance.
Our research activities comprise the numerical modelling of
1 the quantitative analysis of deformation mechanisms (slip and twinning),
2 texture-dependent (macroscopic) flow and localization,
3 prediction of forming limits for sheet metal,
4 mechanical characterization of anisotropic flow, mixed-mode deformation analyses,
5 crimping and dilatation of Mg stent,
6 sequential corrosion simulation (based on Peridynamics) and residual strength analyses (based on finite elements)
for magnesium-based materials. All tasks are accompanied by experimental activities (texture measurements, DIC, SEM) conducted @hereon or designated partners.
- Steglich, D. (2020). "Mixed-Mode Deformation and Failure of a Magnesium Sheet Quantified using a Modified Arcan Fixture." Experimental Mechanics 60
- Steglich, D. and Y. Jeong (2016). "Texture-based forming limit prediction for Mg sheet alloys ZE10 and AZ31." International Journal of Mechanical Sciences 117
- Steglich, D., X. Tian and J. Besson (2016). "Mechanism-based modelling of plastic deformation in magnesium alloys." European Journal of Mechanics - A/Solids 55
- Jeong, Y. and D. Steglich (2020). "Modelling-assisted description of anisotropic edge failure in magnesium sheet alloy under mixed-mode loading." International Journal of Mechanical Sciences 181
- Steglich, D., X. Tian, J. Bohlen, S. Riekehr, N. Kashaev, K. U. Kainer and N. Huber (2015). "Experimental and numerical crushing analyses of thin-walled magnesium profiles." International Journal of Crashworthiness 20(2)
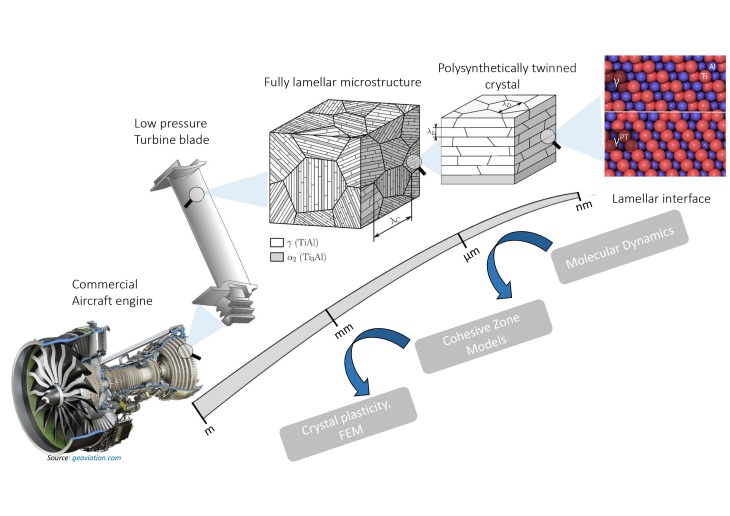
A multi-scale modeling approach of fully lamellar TiAl alloys at Hereon
The civil aviation industry commits to combat climate change by innovating environment-friendly, high fuel-efficient aircraft engines. The quest for novel structural lightweight materials for engine components is at the forefront of research. Gamma-based titanium aluminide (TiAl) alloys are intermetallic compounds, which possess an excellent combination of properties (e.g., low density, high specific strength, and specific moduli); thus, it started replacing the conventional materials in rotating components operating at high-temperature (e.g., Low-Pressure Turbine blades). Continuous efforts are being made to improve the service temperature of TiAl alloys; by optimizing the target microstructure with desired mechanical properties. Four interesting microstructures exist in TiAl alloys, namely duplex, nearly gamma, nearly lamellar, and fully lamellar. Among them, fully lamellar microstructure particularly excels for high-temperature applications. This microstructure consists of two intermetallic phases (γ -TiAl, α2 - Ti3Al), is built up from the atom to the component in several hierarchy levels, from single lamella (nm size) over single colony (µm size) to poly-colony structure (mm size). Various material interfaces make the microstructure extremely interesting and equally challenging: interfaces between lamellae, between domains, and between colonies, see Figure.
The Institute of Material Systems Modeling at Hereon takes on these challenges strategically with its pool of modeling and simulation expertise across the internal departments. Complexity in fully lamellar TiAl alloys stems from the multi-scale nature of hierarchical interfaces contributing to the thermo-mechanical deformation behavior (e.g., fracture, creep). Thus, our multi-scale modeling includes computational methods ranging from continuum (crystal plasticity, cohesive zone models, finite element methods) to atomistic (molecular dynamics); to understand the microstructure-property relationship in TiAl alloys systematically. The desired outcome is a robust, physically sound, microstructure-informed constitutive model capturing the reliable material behavior of TiAl alloys at the component scale; simulated under thermo-mechanical service conditions. To this end, our multi-scale modeling research synergizes the experimental efforts of our partner institutes at Hereon to foster the alloy developments; thus, solving the grand challenge of the aviation industry.
- Hariprasath Ganesan, Ingo Scheider, and Christian J Cyron: Quantifying the high-temperature separation behavior of lamellar interfaces in γ-TiAl under tensile loading by molecular dynamics. Frontiers in Materials, 2020
- Jan Schnabel and Ingo Scheider. “Crystal Plasticity Modeling of Creep in Alloys with Lamellar Microstructures at the Example of Fully Lamellar TiAl.” Frontiers in Materials, 2020
- J.E. Schnabel, S. Bargmann: Accessing Colony Boundary Strengthening of Fully Lamellar TiAl Alloys via Micromechanical Modeling; Materials 10.8, 2017
- J.E. Butzke, S. Bargmann: Thermomechanical modeling of polysynthetically twinned TiAl crystals, Philosophical Magazine 95:24, 2015
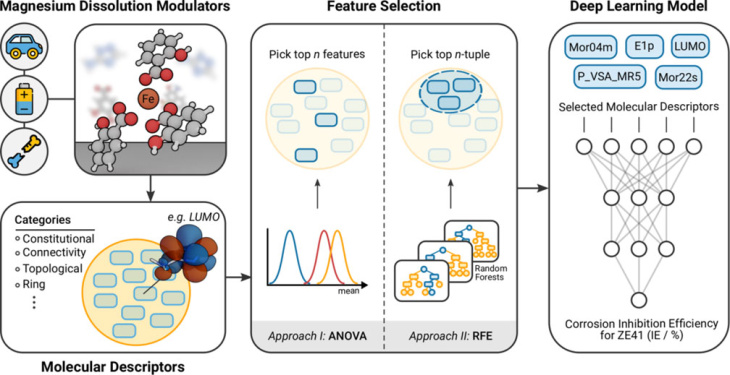
The department for Machine Learning and Data is developing novel approaches to combining the optimization of the topology of artificial neural networks with their training process. This helps eliminating the need for expert knowledge in setting up machine learning architectures, increasing hence their usability for non-experts in data science. Our work on fundamentals of machine learning is complemented by a host of application projects together with both internal and external partners. For example, together with the Hereon-Institute of Surface Science we combine experimental data, atomistic computer simulations and machine learning to identify efficient chemical compounds for corrosion inhibition for magnesium alloys.
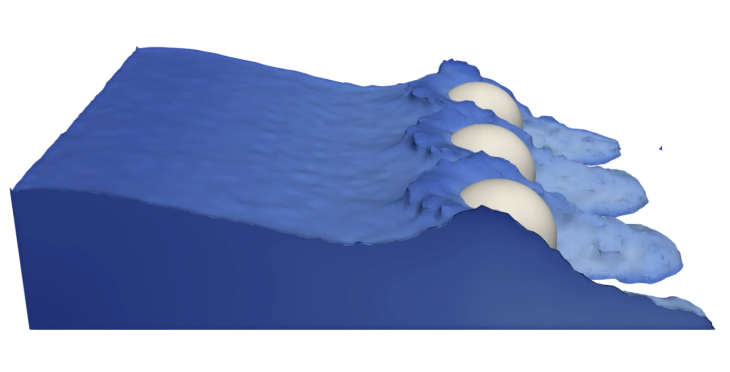
Together with partners from the Technical University of Munich (Prof. W. A. Wall) , Germany, the Bundeswehr University Munich (Prof. A. Popp), Germany, and Uppsala University (Prof. M. Kronbichler), Sweden, we are developing research software for multiphysics simulations of complex systems relying on advanced C++ libraries for high performance computing (HPC) such as Trilinos or deal.ii. We use this software for the development of digital twins for various applications including aerospace engineering, renewable energies, biomedical engineering and materials science.
UMATs are ABAQUS-run programs which contain a user-defined material model.
UELS are self-defined finite elements, which are not part of ABAQUS distribution.
The development of the UMATS for the different types of models described below was accomplished in our institute. Those which are no longer in the test-stage but whose numeric stability and applicability on structures have been verified, may at this stage be acquired by us. The UMATs cost 1000 Euro/UMAT for universities/research institutes. Specaial rates for industries are available.
The UMATS deal with the following programs with documentations:
GTN Model: Rate-dependent formulation of the Gurson, Tvergaard and Needleman models for ductile metals (isotropic hardening). Guidance on the use of these models is available here as a pdf-document and is free to download.
GTN Model: Rate-independent formulation of the Gurson,Tvergaard and Needleman models for ductile metals (kinematic hardening).
Rousselier Model: "Phenomenological " damage model for ductile metals.
Cohesive zone element: able to describe material separation using different traction-separation-laws.