Institute of Material Systems Modeling
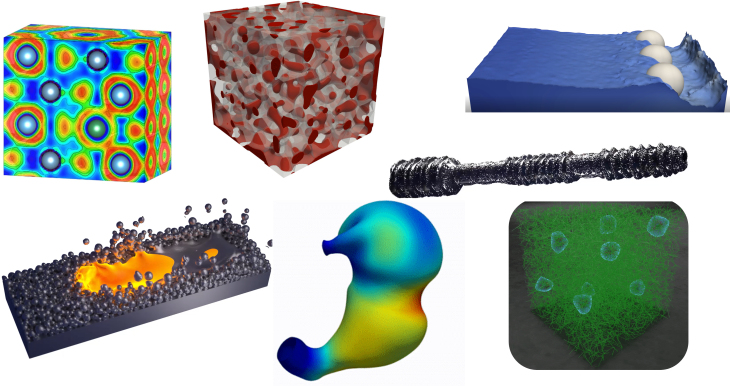
(c): V. Ivannikov, A. Chandran, D. Steglich, J. Eichinger, Hereon; S. Fuchs, M. Henke, TUHH
Developing new materials is a complex undertaking. In addition to pure materials research, manufacturing processes must be developed and complete systems defined. The Institute of Material Systems Modeling works on comprehensive digitalization of all these areas. Compared to the usual experimental procedures, this computer-driven approach promises a deeper system understanding and significant savings in both time and cost. For this purpose, the institute develops innovative methods and software. Through an atomistic simulation team and one for continuum simulations, the entire spectrum of computer simulations is covered, from the atomic to the macroscopic level. A machine learning team augments this spectrum by a data-driven perspective.