No more rivets
Hereon scientists have succeeded in developing an innovative welding process. It saves resources and makes the use of rivets obsolete. The aircraft parts produced with it are thus significantly lighter and lead to lower CO2 emissions during operation. The so-called refill friction stir spot welding was used for the first time for a load-bearing aircraft component as part of the AVaiL-DE project funded by the German Federal Ministry for Economic Affairs and Climate Action (BMWK) and demonstrates great potential for use in a more climate-friendly aviation in the future.
Aviation is to become CO2-neutral worldwide by 2050. Researchers from the Helmholtz Zentrum Hereon have now succeeded in taking a big step in this direction: at the Institute of Materials Mechanics, they have developed an environmentally friendly and versatile welding process that makes the use of rivets superfluous. As part of the AVaiL-DE project funded by the Federal Ministry for Economic Affairs and Climate Action (BMWK), the so-called refill friction stir spot welding was used for the first time to join a load-bearing aircraft component validator. Together with Airbus Aerostructures, the project team produced a so-called sheet metal frame for the Airbus A330. The sheet metal frame is a load-bearing component of which more than a hundred are installed in the fuselage of the aircraft, thus reinforcing it.
![Detail of refill FSSW welds on one of the reinforcements of the A330 lower shell frame. [Photo: Hereon/ Roos] Rahmenspant](/imperia/md/assets/main/transfer/communication_media/2023/fittosize_730_0_dac869755388132a3a7e9c0088505005_pxl_20221130_133733911.portrait-2.jpg)
Detail of refill FSSW welds on one of the reinforcements of the A330 lower shell frame. [Photo: Hereon/ Roos]
Aircraft fuselages consist of many individual metallic parts, which are mainly made of aluminium. In order to increase e.g. strength, hardness and corrosion resistance of the aluminium, it is mixed ("alloyed") with small amounts of e.g. copper, magnesium or zinc during production. The individual parts made from these dissimilar aluminium alloys are difficult or impossible to join together into components using conventional fusion welding. Using the new process, the researchers within AVaiL-DE have now been able to reliably weld individual parts made of the dissimilar alloys into a sheet metal frame.
Moreover, the refill friction spot welding allows the complete elimination of riveting. In addition to saving costly manufacturing steps and supplementary raw materials, such as the rivets themselves, the gap between the component and the rivet, which is susceptible to the formation of cracks and corrosion, is also eliminated. The aircraft fuselage thus becomes lighter and saves valuable resources already during production.
"Modern solid-state joining technology, as used here in the refill friction spot welding, is a key technology for enabling resource-efficient and thus more climate-friendly mobility through innovative lightweight design”, says Dr Arne Roos, Group Leader at the Hereon-Institute of Materials Mechanics.
Even though the researchers have proven that the process works without problems in the laboratory, it will still take a few years until it has passed the extensive qualification processes for series production in aircraft manufacturing.
It's about the point
The environmentally friendly refill friction stir spot welding (refill FSSW) is technically classified as a pressure welding process and works according to the following principle:
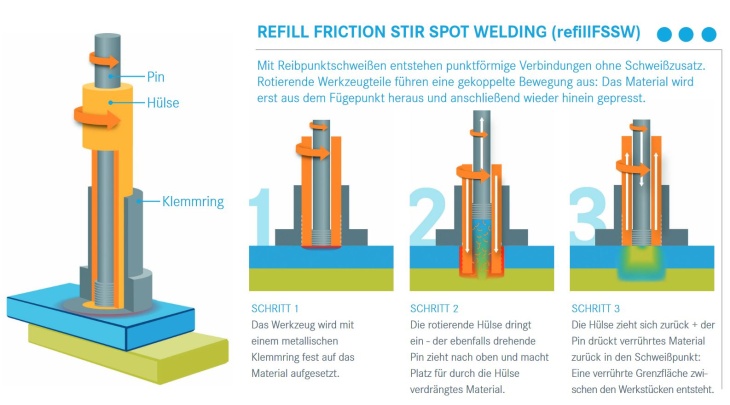
Inside a clamping ring are a rotating sleeve and a rotating pin. While the rotating sleeve penetrates the materials to be joined, the pin pulls upwards and creates space for the softened plasticized material displaced by the sleeve (see illustration). In the next step, the sleeve pulls up while the pin lowers again and presses back the "stirred" material: The result is a point-like connection without melting, sparks or vapours.
Further information
Contact
Group Leader
Phone: +49 (0) 4152 87-2071
Institute of Materials Mechanics
Helmholtz-Zentrum Hereon
Press Officer
Phone: +49 (0) 4152 87-1784
Communication and Media
Helmholtz-Zentrum Hereon