The Benefits of AI in Materials Research
Not only Google and Facebook use artificial intelligence methods. Neural networks and self-learning programs also increasingly come into play in materials research. At the Helmholtz-Zentrum Hereon, such methods assist in tailoring future hybrid materials and in developing new implants.
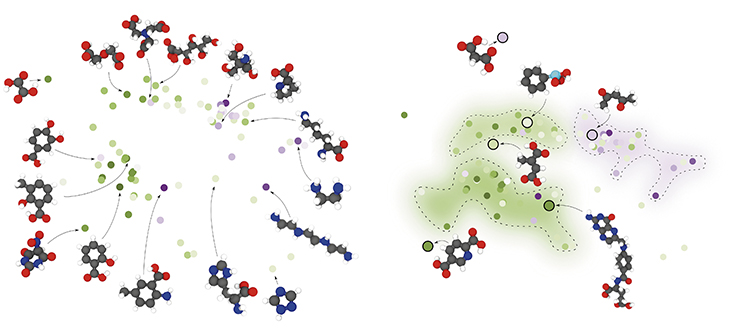
This simulations shows the scientists how well these molecules could serve as corrosion protection. Copyright: Robert Meißner
You could actually mistake it for an abstract piece of art – colourful surfaces and bright speckles that clump into small heaps in some areas. But take another look: “That is a type of map,” says Prof Robert Meißner from the Hereon’s Institute of Materials Research. “Every speckle represents a different molecule and signals how well this molecule could assist in corrosion protection.” The graphic is the result of an adaptive algorithm and represents a trend in materials science: artificial intelligence (AI) methods are increasingly finding applications here.
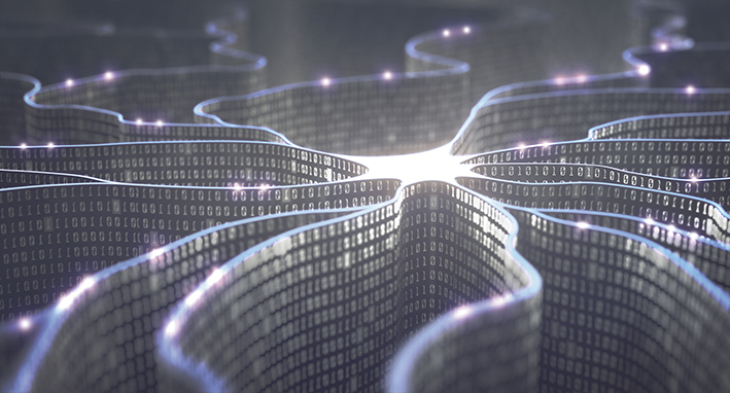
Copyright: istockphoto/ktsimage
Computer simulations have already played a vital role in materials research for quite a long time now. If there is a desire, for example, to develop a new metal alloy, the computer can first simulate it. This is how experts can obtain initial clues about the alloy properties and can then tailor their experiments in a considerably more targeted manner. With artificial intelligence there is a new tool available to the professional community: on the one hand, it can help immensely in accelerating computer simulations and therefore make them more efficient. On the other, neural networks and deep learning programs can reveal connections that would otherwise remain hidden: how do the properties of a material depend on their microscopic structures—for example, on its crystal lattice?
Robert Meißner uses these new techniques to recreate materials virtually from scratch: he simulates on the computer how individual atoms, together with their electron sheaths, behave in a molecule – and by doing so, he deduces its properties. He, for instance, devotes his time to small organic molecules with an interesting property: they can inhibit corrosion in magnesium, a lightweight engineering material. “You could, for example, add them to a protective lacquer,” explains Meißner. “If it gets scratched, these molecules could then be released and could render corrosive substances harmless.”
Artificial Intelligence for Corrosion Protection
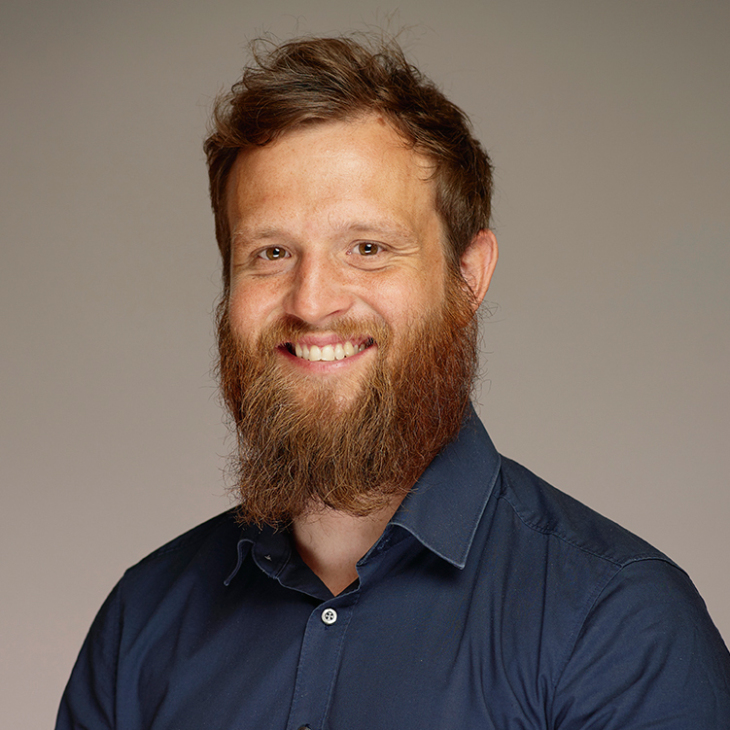
Prof. Dr. Robert Meißner. Foto: Hereon/Christian Schmid
There’s a catch though: which molecules are particularly suitable here? In the laboratory, this question could only be cleared up through a great deal of effort and numerous series of measurements. This is why Meißner and his team developed a computer simulation based on artificial intelligence. On the one hand, the researchers fed into the software the molecular structures of approximately two hundred substances. On the other, they included data from experiments that describe the chemical behaviour of the respective molecules.
Based on this data, the adaptive algorithm created a molecular map with coloured areas and speckles. The map shows similar molecules in neighbouring regions. Some are anti-corrosive, while others accelerate corrosion. “In principle, the method works, but the errors are still pretty extensive,” says Meißner. The method, however, is greatly promising for the future. This is because, in principle, the AI software can also sort molecules on the map for which there is no measurement data yet available. “This allows us to estimate which molecule is especially promising,” says Meißner, hopefully. “This could be a vital clue for chemists to study this particular molecule more closely in the laboratory.”
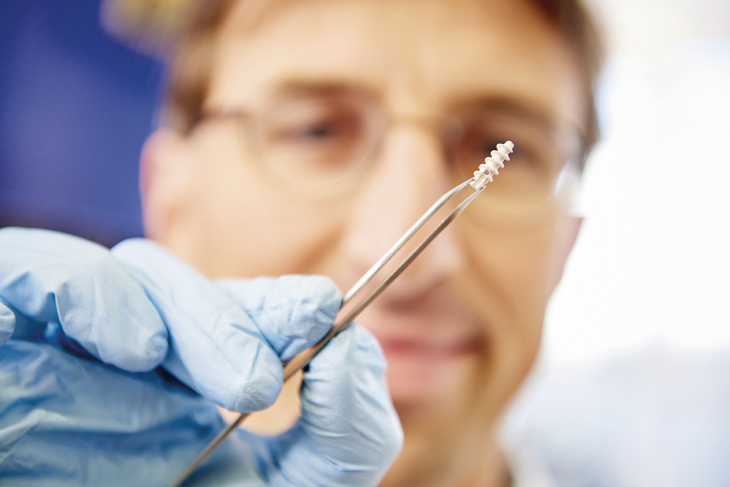
This magnesium bone screw is biodegradable, rendering a second operation for removing the imolant unnecessary. AI helps in understanding the different contexts. Photo: Hereon/Christian Schmid
There is also another research field in regard to magnesium that benefits from artificial intelligence methods. The team led by Regine Willumeit-Römer develops implants made of this lightweight metal in the division for “Metallic Biomaterials”. Screws, nails or plates made of magnesium could one day repair broken bones so that they fuse together again. Stainless steel or titanium implants have so far been used for this application. They, however, must be removed again after the bone heals, causing a strain on the patients. In contrast, implants made of magnesium would entirely dissolve in the body without the need for further surgery.
Support Using Self-Learning Software
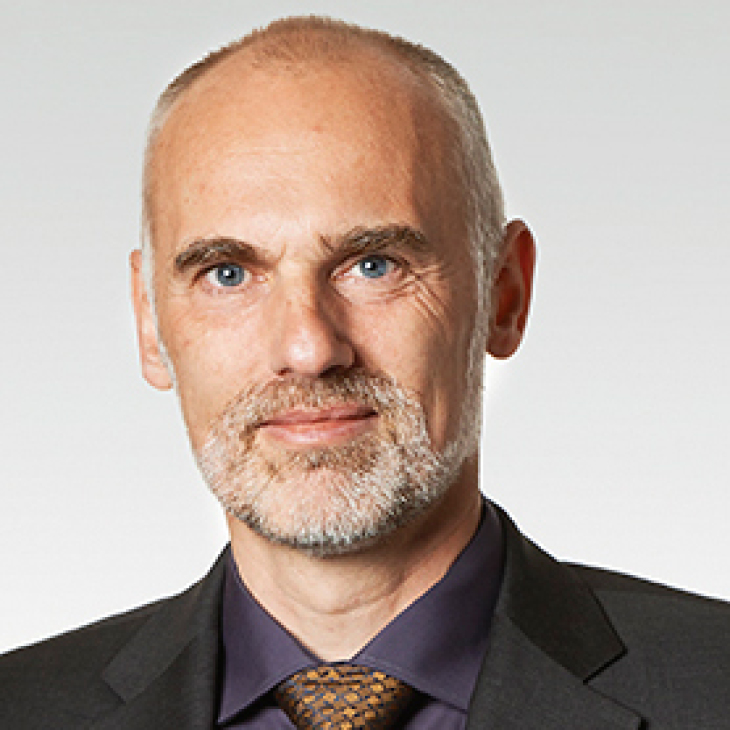
Prof. Dr. Norbert Huber. Photo: Hereon/Christian Schmid
The method is still in the research phase. The experts must, for example, determine how quickly and under what conditions magnesium dissolves in the body. The problem is that a living organism is a highly complex environment. It is teeming with so many different molecules, such as CO2, oxygen, minerals and proteins—and they could all influence the magnesium’s degradation. In order to determine what role each of the different molecules plays, researchers would need to set up numerous series of measurements—this is time consuming and very expensive in practice.
But then the team received support: Prof Norbert Huber, head of the Materials Mechanics Department, provided his assistance. Together with his team, he programmed a neural network and carefully trained it using selected measurement values. “Initially we determined that our software can quite accurately predict the rate at which the magnesium corrodes in the body,” Huber explains. This laid the groundwork for an array of virtual experiments: the experts systematically removed certain parameters such as concentrations of CO2 or sodium chloride—that is, common salt. The software then provided information on how a missing parameter affects the corrosion rate. In addition, the researchers “fed” the neural network with just one parameter and observed what the program made of it.
The result was astounding: the calculations showed that the CO2 content is much more important for corrosion than was expected,” says Huber. “We earlier presumed that sodium chloride was the main cause of corrosion.” Closer analysis showed that the interplay between the two parameters is the definitive factor: it is the combination of salt and CO2 that decisively determines the corrosion rate—an insight with which further experiments can be much more effectively and selectively planned.
The special aspect of the project is that, in contrast to many other AI applications, it didn’t require a great quantity of data to train the software. “In this case, a relatively small quantity of high quality data with little variance was sufficient,” says Huber. “We provided the software with a lot of prior knowledge. This reduced the complexity of the problem so that we managed with less training data.”
Corrections Through Learning Algorithms
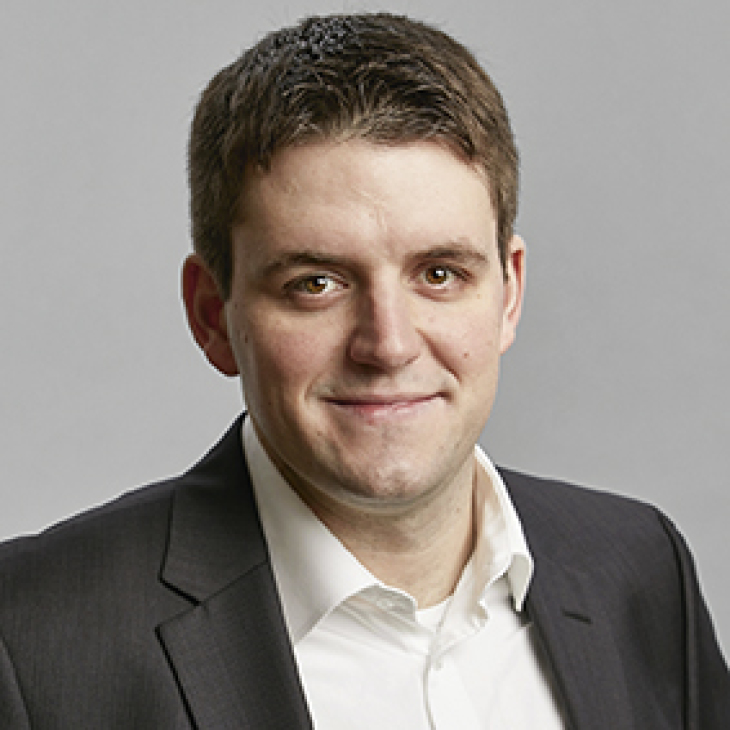
Prof. Dr. Benjamin Klusemann.
Photo: Brinkhoff-Mögenburg/Leuphana
The departments for “Solid State Joining Processes” and “Laser Processing and Structural Assessment” also profit from AI methods—for example, when optimising a method that increases the lifespan of lightweight components. In “laser shock peening”, a laser fires short light pulses at a metal, locally vaporising part of the surface. Starting from this vaporised surface, shock waves emanate through the material and change its properties. “We can thereby modify the residual stresses in the metal,” explains Prof Benjamin Klusemann, head of the Solid State Joining Processes Department.
Residual stresses arise commonly when manufacturing and processing a component. If, for example, a sheet is bent during a rolling process, it then displays a certain “tensioning” even when it is not longer loaded. These residual stresses are not necessarily a disadvantage. Under certain circumstances, they can be used to retard the generation and propagation of short and long cracks and thereby increase a component’s lifetime, such as on an aircraft wing. Laser shock peening can modify the material’s residual stress in such a way that it can withstand higher loads. In an ideal situation, it increases the lifetime of a component up to fourfold.
To optimise the method, the Hereon scientists use computer simulations. Here the computer virtually simulates the entire process—from the impact of the laser pulse and the propagating shockwaves, to a prediction of the crack growth in the laser-treated material. “These simulations help us understand the influence of individual process parameters as well as the underlying mechanisms,” says Klusemann. “We can, for example, use this to better adapt the method to a specific application.”
In order to create as realistic simulations as possible, the experts must compare the simulations with data obtained from experiments: how large are the residual stresses after laser treatment in reality? In order to address this question, a drill is used to create small holes in the laser peened component. The researchers measure how the surface deforms as theresidual stress decreases. From this measurement data, they can then calculate back to the size and direction of the residual stresses.
The problem is that this reconstruction leads to errors at high stresses. Normally time-consuming computer calculations are necessary to correct these errors later, which can take days. To speed up these corrections, adaptive software based on a neural network has been developed at Hereon. “It can predict in a short period of time which corrections are necessary,” says Klusemann. “In principle, it could be utilised in real time, so the result would already be available while drilling.”
The necessary requirement is that for the AI to provide reliable results, it needs to be trained with appropriate data. “If artificial intelligence is trained with inaccurate data, we get inaccurate results,” says the researcher. “It is extremely important that we evaluate how reliable the results are that we obtained through the assistance of artificial intelligence.”
Computation Acceleration with AI
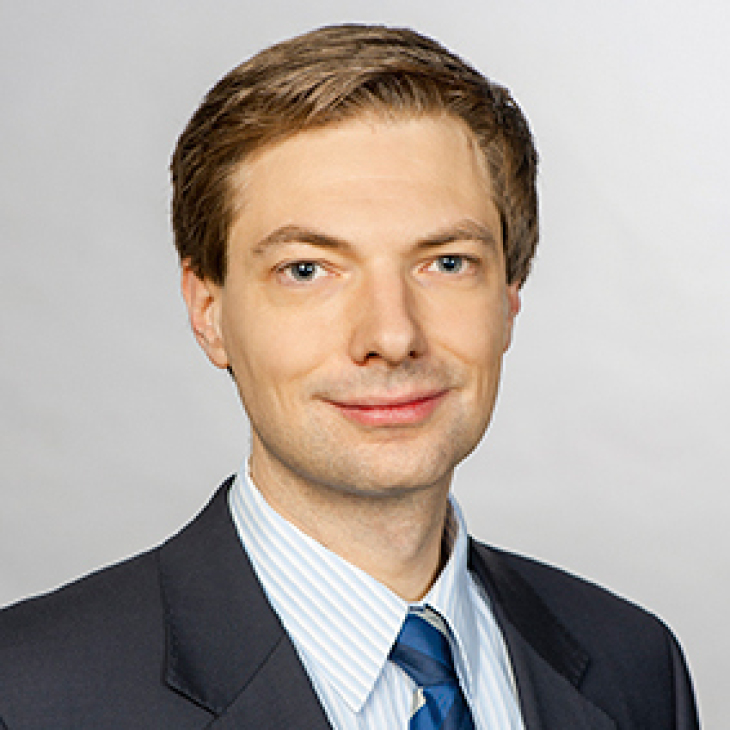
Prof. Dr. Christian Cyron. Photo: TU München
The department for “Simulation of Solids and Structures” also places their hopes in artificial intelligence methods. Prof Christian Cyron and his team study, for example, how compound materials can be optimised. If, for instance, the rigidity of a soft, rubbery material increases when small hard particles are embedded , how then does this rigidity depend on the form and size of the embedded particles? “In order to simulate this on the computer, you would actually need to calculate all possible particle forms,” Cyron says. “This would really take far too long.”
So the experts use a different strategy: they run their simulations only for a limited number of particle sizes and forms. Using the results of these calculations, they then feed a deep learning algorithm. This algorithm can extrapolate the available data and is able to estimate the extent of rigidity that would result for other particle types that were not contained in the training data. “This is actually not as precise as an exact simulation,” says Cyron. “But for our aims, we can live with an inaccuracy of a few per cent.” These methods ultimately serve, above all, as a preliminary selection: which particle types are of further interest to research? Which ones can we disregard?
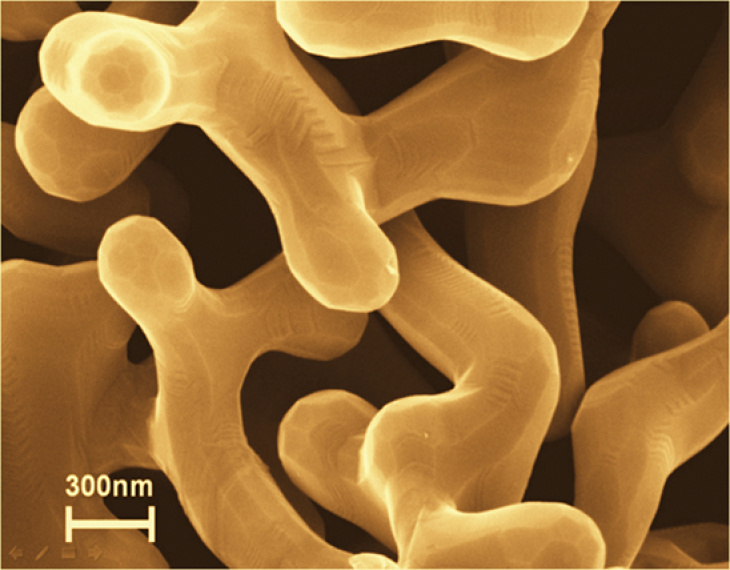
Nanoporous gold is an exciting material for applications in areas such as sensor technology. Photo: Haijun Jun
The experts have developed their adaptive algorithm with the help of fictitious example materials. They now wish to apply it to a real, promising class of materials: nanoporous (sponge-like) metals which combine low weight with high internal surface. This makes them interesting for applications such as in the field of catalysis or in sensor technology. The plan is the following: the researchers initially wish to carry out conventional computer simulations, which they will feed with data from high-resolution microscopes as well as from experiments that measure material properties. Using the results, they then wish to train the artificial intelligence. “By doing so, we want to predict the properties of the nanoporous metals more quickly than is possible through conventional simulations,” Cyron says, hopefully. “Using machine learning, we can considerably accelerate computer simulations and process their results more quickly.”
Lastly, AI could thereby provide clues as to how we can tailor a material—creating a kind of machine-intelligent material design. “We are still pushing forward, and no one can even say where this journey will lead or how useful these new methods will be in the end,” says Cyron. “Artificial intelligence is really no magic bullet, but could serve as a vital tool in helping to solve fundamental problems in the field of materials research.”
Author: Frank Grotelüschen
Published in in2science #8 (Juni 2019)